汽車覆蓋件及其模具零件型面面積大、造型特征復雜,嚴重制約模具鉗工的研合效率,而模具研合精度直接影響制件的表面成形質量。交付模具周期與覆蓋件表面質量已成為主機廠衡量模具企業(yè)技術水平的兩大重要指標。
隨著時代的發(fā)展與科學技術的進步,越來越多的計算機模擬輔助軟件被應用到模具制造及加工中。通過AutoForm軟件模擬成形過程,分析板料在成形過程中各個區(qū)域的變薄情況,根據不同區(qū)域變薄量來補償模具零件各區(qū)域的偏差間隙,取代傳統(tǒng)依靠鉗工研合經驗來補償模具零件型面間隙,更加精準地完成模具零件型面各區(qū)域的間隙偏差補償,實現(xiàn)在合模過程中模具閉合時模具型面與制件完全貼合,減少了鉗工手工修改模具零件型面的工作量,提升了模具研合效率,實現(xiàn)效率與制件成形質量的雙重保證。
汽車模具研合現(xiàn)狀
1
模具零件型面的研合精度直接影響外覆蓋件的表面成形質量及尺寸精度,故主機廠對模具驗收的研合要求也是模具移交的重要指標之一,合資及國產品牌主機廠對重要的模具零件型面要求研合率均要大于95%。
行業(yè)的高標準、高要求促使模具制造企業(yè)不得不投入更大的人力、物力和財力去提升企業(yè)的技術水平,縮短模具的研合工時,減少模具制造成本是提高企業(yè)在模具行業(yè)中競爭力的重要途徑。
表1 覆蓋件拉深工序研合標桿工時
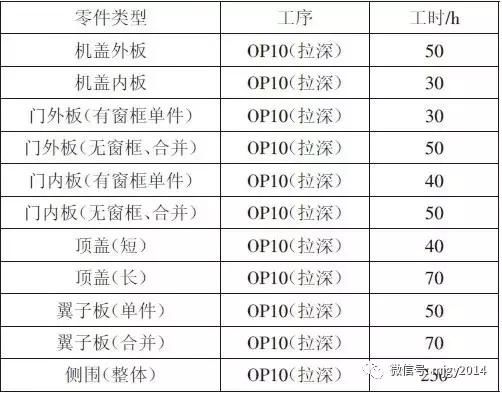
某中日合資模具制造企業(yè)給出的各類型車身覆蓋件研合所需的標桿工時如表1所示,單工序拉深研合工時長,有較大的提升空間。
影響研合工時原因分析
2
影響模具零件型面的研合工時因素有:
01
模具零件材質,不同的材料在長時間的放置后會發(fā)生去應力變形,變形量不一致。
02
數(shù)控機床的加工精度,高精度的機床能減小模具零件型面的加工偏差。
03
制件結構,側圍等大型覆蓋件的研合工時會大于機蓋等。
04
模具在壓力機上的受力變形,不同壓力機的壓力不同,引起的模具零件變形量有較大差異。
05
制件型面的角度差,由于特征造型需要,不同區(qū)域與沖壓方向形成不同的角度,多角度的存在也增加了研合難度。
06
板料在拉深過程中的變薄,制件各區(qū)域的料厚均小于原始厚度且料厚不均等,直接導致模具閉合瞬間板料和模具零件型面不能同時接觸,局部區(qū)域出現(xiàn)離空現(xiàn)象。
提升模具研合效率的常規(guī)對策
3
針對模具零件材質產生的去應力變形而導致模具零件型面研合困難,主機廠和模具制造生產商對模具各部件材質的選用已有自己的參考標準,如表2所示。
表2 模具材質
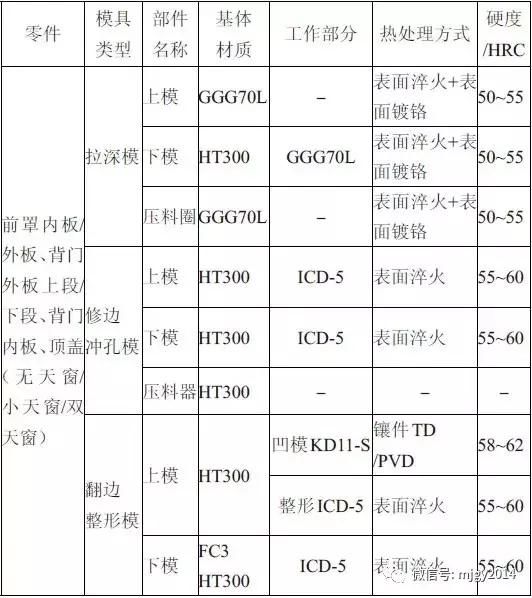
針對模具在壓力機上的受力變形而導致模具零件型面產生間隙偏差,許多企業(yè)已重視并有了相應的改善措施,通過Jstamp和AutoForm軟件分析模具在壓力機上的受力變形,將模具零件型面各區(qū)域的變形量用階梯線與數(shù)值直觀地展示,如圖1和圖2所示。
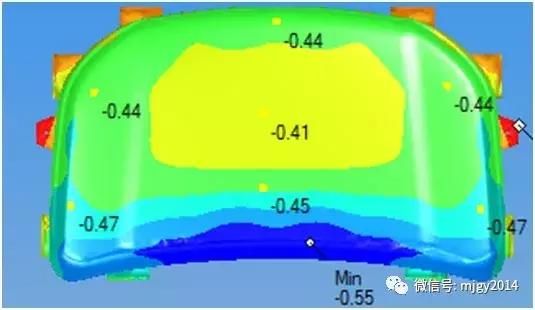
圖1 Jstamp計算凸模變形量
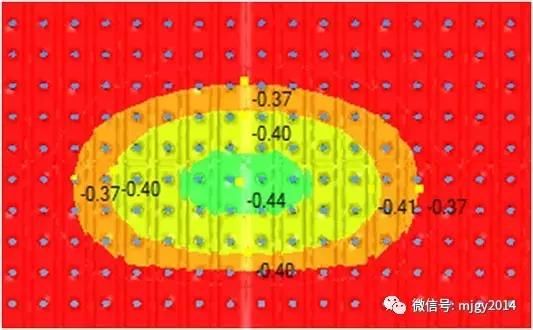
圖2 Jstamp計算模具變形量
通過提取模具零件變形階梯邊界線與變形量,采用UG或CATIA軟件將變形量補償?shù)郊庸?shù)模,消除因模具受力變形而導致的模具零件型面高度差,提升鉗工的研合效率,減少鉗工的研合工時。
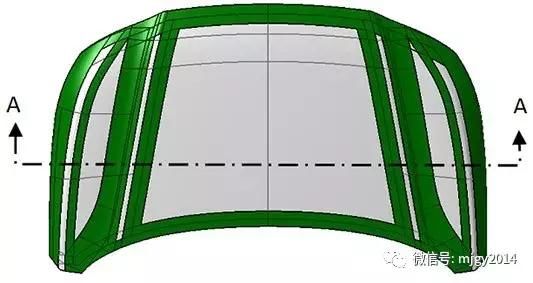
圖3 機蓋研合要求
針對制件型面角度差導致的研合難度,以某機蓋外板為例,黑色部位為要求有研合的型面,灰色部位無研合要求,如圖3所示。由于側壁面及凹成形區(qū)域的存在,截面上各區(qū)域零件型面的切向角度與沖壓方向均存在不同的角度差,如圖4所示。
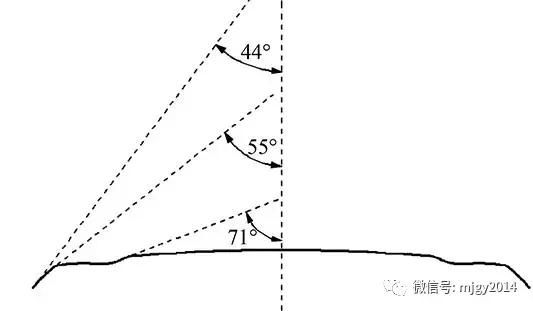
圖4 橫截面角度差(圖3A-A)
制件型面角度差的存在導致在上、下模合模過程中不同角度區(qū)域型面間隙存在差異,如圖5所示,上模到底前20mm時,側壁的型面間隙為15.61mm,常規(guī)的工藝會結合以往研合經驗,根據不同的區(qū)域進行相應的強壓(零件型面偏差加工)處理(見圖6),以減小或消除角度差導致的型面偏差,確保上、下模各區(qū)域型面同時接觸板料。
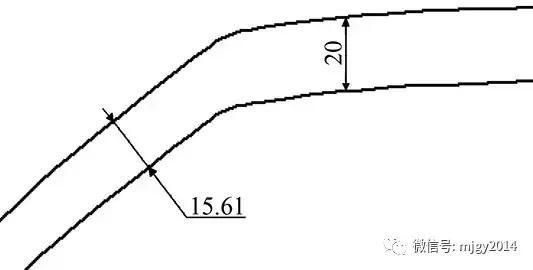
圖5上模到底前20mm型面間隙
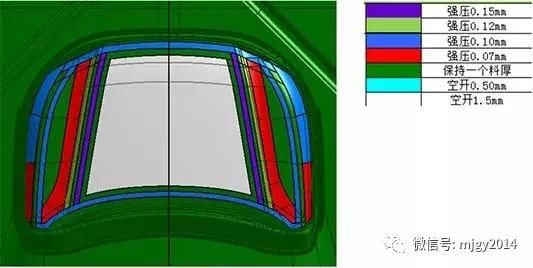
圖6 機蓋外板強壓工藝
但強壓工藝有一定的局限性,只考慮型面角度差帶來的間隙偏差,并沒有考慮板料在拉深過程中變薄而帶來的研合間隙偏差,且依靠經驗設置強壓值并不能解決所有零件的偏差,故該方法不能徹底消除間隙偏差導致的研合困難。
虛擬合模技術的應用
4
現(xiàn)引入虛擬合模的概念,通過AutoForm軟件分析板料成形過程中各區(qū)域的變薄情況,模擬模具閉合過程,根據板料各區(qū)域的變薄量及角度差制定相應的強壓工藝,替代依靠經驗設置強壓工藝,能更加精準控制型面各區(qū)域的間隙。
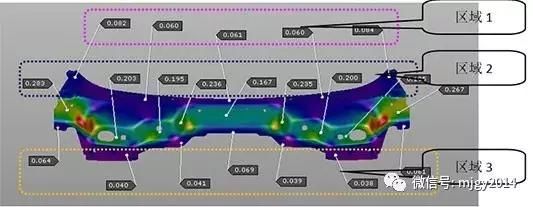
圖7 零件成形變薄量
以某汽車搭接件闡述虛擬合模的概念及應用,第一步采用AutoForm分析板料在成形過程中的各區(qū)域變薄量t,如圖7所示,制件變薄梯度主要分3個區(qū)域,區(qū)域1板料變薄量約0.06mm、區(qū)域2側壁板料變薄量約0.16~0.28mm、區(qū)域3法蘭邊板料變薄量約0.04mm。
第二步以區(qū)域1的板料變薄量作為參考基準值η,擬定在區(qū)域1對應的上模零件型面進行η=0.06mm的強壓補償,采用AutoForm軟件模擬上模閉合到底前0.06mm時各區(qū)域模具零件型面的間隙離空值h,用GOMinspect軟件將其呈現(xiàn),如圖8所示。
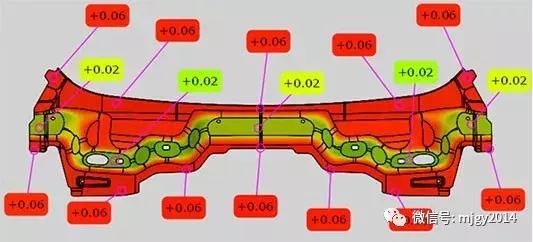
圖8 模擬上模到底前0.06 mm各區(qū)域模具型面間隙
上模到底前0.06mm時,區(qū)域1與區(qū)域3的模具零件型面間隙離空值為0.06mm,由于角度差的存在,區(qū)域2側壁零件型面離空值為0.02mm。由此可知,在不考慮板料變薄時,當區(qū)域1與區(qū)域3進行0.06mm的強壓時,區(qū)域2側壁只需要進行η-0.02mm=0.04mm的強壓即可滿足各區(qū)域制件同時接觸模具零件型面。當考慮板料變薄因素時,得出強壓設置公式θ=-t+η-h來滿足各區(qū)域型面的間隙要求。
區(qū)域1最終的強壓值:θ=-0.06+0.06-0.06=-0.06mm
區(qū)域2最終的強壓值:θ=-(0.16~0.28)+0.06-0.02=-(0.12~0.24)mm
區(qū)域3最終強壓值:θ=-0.04+0.06-0.06=-0.04mm
其中,θ為上模零件型面所需的強壓量;t為板料成形后的變薄量;h為在初始參考基準值下上、下模零件型面的離空數(shù)值;負號表示強壓是向下模側置補償。
第三步通過UG或者CATIA軟件將各區(qū)域強壓量補償?shù)郊庸?shù)模,完成補償?shù)募庸?shù)模各區(qū)域型面的強壓值如圖9所示。
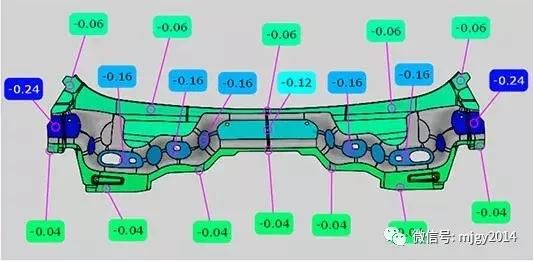
圖9 型面偏差加工強壓值
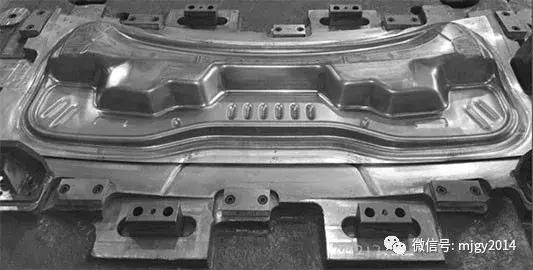
圖10 現(xiàn)場實際研合效果
該制件運用虛擬合模技術后的研合效果如圖10所示,拉深模在研合8h后模具零件型面研合率已達到90%以上,成功縮短研合工時,提高了研合效率。